I'm really enjoying the West Kelowna Pick-n-Pull!
We ended up heading out to Kelowna again for a short visit, and while I was there I checked out Pick-n-Pull again, and walked out with a wallet $30 lighter. What did I buy, you ask?
A brand new, partially installed convertible top. It looks like the owner of the car tried to install the top themselves without the correct tools, got frustrated, and junked the car. I had to pop about 40 staples to get the top off the car which as easy, since they used a standard staple gun rather than a more powerful upholstery stapler to attach the top.
For comparison, a new top with a plastic rear window (I wanted glass, but I'm not going to argue) is $240 and up from online vendors. I think I did fine.
Out of hibernation for another year
I brought the car out of storage (in my back yard) this week. I forgot how fun it is to drive. Other than pumping up the front drivers side tire and charging the battery, everything was ready to go. I disabled the fuel injectors and ignition, cranked the engine until I saw oil pressure on the gauge, and it started right up. During the course of the winter a little more rust showed up, but I have plans to take care of that this year.
A successful junkyard run out in West Kelowna
While I was on vacation in Kelowna, BC for 2 weeks visiting my in-laws, I took a morning to go check out Pick-n-Pull and see if I would have any luck.
I had excellent luck. a 1994 LeBaron GTC donated the header bow and top latch assembly I so desperately needed. A 1988 Daytona Shelby Z donated a cruise control bracket which will clear the intercooler, and a 1987 LeBaron donated a rear trim piece and one of the rear ashtrays I was missing. The total? $39.75, plus $28.50 to ship the stuff back to myself on the bus.
I had excellent luck. a 1994 LeBaron GTC donated the header bow and top latch assembly I so desperately needed. A 1988 Daytona Shelby Z donated a cruise control bracket which will clear the intercooler, and a 1987 LeBaron donated a rear trim piece and one of the rear ashtrays I was missing. The total? $39.75, plus $28.50 to ship the stuff back to myself on the bus.
Well, it's been a long time
The performance upgrades (intercooler, keeping boost under control) worked very well for a couple of weeks, then I noticed things weren't as fun as they once were. Now that I can hold high boost levels without hitting cut-out for extended periods of time, the stock clutch is giving up.
I also have some dash wiring issues to check out as the Traveler (trip computer) lost its memory a few times, and I've seen the airbag light flicker. Both indicate to me I might have a bad ground.
Finally, the drivers side top latch broke apart and won't re-latch securely, and the part that needs to be replaced requires removal of the top fabric so it looks like I need to replace the top sooner rather than later. I also need to hunt down the complete front header and both latches as an assembly which sounds easier than it is because hardly anyone sends convertibles to the junkyard around here.
Floorpan welding - part 2
Floorpan welding - part 1
Had I discovered all the rusty metal I needed to replace at once, I probably would have begun searching for another LeBaron and turned this one into a parts car. Fortunately for this particular LeBaron I did not. It wasn't until I had gone far into the welding that I discovered how much work I was looking at.
The next step was to whip my welding skills back into shape. I last welded about 12 years ago, using a DC arc welder, on 1/8 to 1/4 inch mild steel. I picked up a portable MIG from Princess Auto for $129, and tried to re-learn how to weld on 22-gauge steel. A few evenings of blasting holes no matter how careful thought I was yielded a technique that worked for me. Very, very short blasts. For $129 you don't get the best welder out there, and all I had was a 70/90 amp switch. People will tell you 70A is far too much for 22 gauge steel, and they're probably right. I made it work.
I also invented a new art form. I call it "sheetmetaligami" where I fold complex shapes out of sheetmetal then weld them together to form a larger object.
It's alive!
Maybe now that I can get out of the garage I can back-fill some missing posts about my progress.
The mighty LeBaron is moving under its own power. And power it has! Much, much better than before. There were a couple of times while I was doing the 20-mile breakin where I kinda scared myself.
It's still fun.
The mighty LeBaron is moving under its own power. And power it has! Much, much better than before. There were a couple of times while I was doing the 20-mile breakin where I kinda scared myself.
It's still fun.
I can assure you, Mr. Flintstone, that you will find driving my car difficult now.
I've been held up with welding recently, the engine is still not in the car. I knew I had a couple of small holes in the floorpans around the parking brake cable, but when I lifted the carpet and did some poking I discovered that I had a lot of work ahead of myself. The major holes in the drivers side are almost finished, then I have a few more minor holes here and there. Everything is getting a good coating of rubberized undercoating goop to seal it, from above and below once I'm done. Hopefully I never need to do this again.
Past the point of no return
I sold the engine and transmission the day after I pulled it, and now the computer and engine bay wiring is also sold. At this point it's now easier to complete the turbo conversion than it would be to try to go back to TBI.
Rebuilding a turbocharger - Part 2
Oil up the new bearings and slide them into place. There was a noticeable difference between how the old and new bearings fit. It is interesting to note that the original bearings look like aluminum and the replacement bearings are bronze. Replace the outer snap rings, set the new thrust bearing in place on the locating pins and replace the center cartridge-to-compressor backing plate o-ring. Set the center cartridge aside and let's work on the compressor backing plate.
That springy thing retains the thrust bearing. It should come out easily with gentle prying. The new one takes a little more effort to install, I used the old thrust bearing to press mine into place. The compressor oil seal is a 4-piece assembly on these turbos. As you remove it keep track of how it fit together, and remember there's a spring behind it all. Once you replace the seal and the thrust bearing retainer, you can bolt the backing plate back on the center cartridge.
Since I haven't found a good torque spec for the compressor wheel nut, I tightened it to "about as tight as the original felt". Highly scientific, I know. Don't forget to line up your index marks you made before tightening the nut.
Rebuilding a turbocharger - Part 1
No point putting in a new engine with an old turbo that's been beaten on just so the turbo can leak oil all over because the bearings are shot, when a full rebuild kit can be had for $120 shipped to Canada from G-Pop Shop. This series will cover disassembling and reassembling a turbo, and show you just how easy it is.
Okay, maybe it's not that easy, at least not the disassembly part. Think about it -- these turbos are 20 years old and have been subjected to exhaust heat, and their own heat generated from spinning amazingly high RPM.
First, a shot of our victim: A Garrett T03, in this configuration known as the "Turbo II" turbo. The stock Mitsubishi TEO4H is on the right... you can see why the Garrett is a better choice for performance. Sure, a larger turbo will take longer to spool up, but when it does, hang on to your pants.
The first step was to remove the "swingvalve", which includes the exhaust outlet. This Garrett has the larger 2 1/2 inch exhaust opening, instead of the 2 1/4 inch opening in older models. There are 5 bolts holding the swingvalve to the turbine housing, one is hidden inside the swingvalve. I lucked out and all came out with a little penetrating oil. The general consensus seems to be that you require heat to get the bolts out without snapping them off.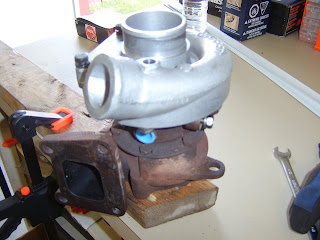
After removing the swingvalve and realizing I had no vise to mount the turbo in, I bolted it to a 2x4 which I could clamp down to the workbench through 3 of the swingvalve holes. This is where the fun begins. There are 6 bolts that hold the centre cartridge (including the shaft and bearings) to the turbine housing. These are usually the worst bolts to remove, and clearance is quite limited. I managed to get a thin box-end wrench on 3 of them, the other 3 need an open-end wrench. I soaked the bolts in penetrating oil for quite a long time. I sprayed them daily for several weeks, because again the general consensus is that heat is required for all 6 bolts, and that the housing needs to be heated cherry-red before you can even think about removing them. That cuts out your garden variety propane torch as a source of heat.
Somehow I again lucked out and 5 of the 6 bolts came out without problem, and without heat. Wouldn't you know it, though, that the one bolt that had to be stubborn was one of the ones that needed an open-end wrench. A little heat helped break it free, but nowhere near the amount of heat to turn the housing any colours.
With the bolts loose, the next step is to separate the centre cartridge from the turbine housing, usually 2 of the bolts line up on the coolant fitting bosses, and you can turn these bolts out a little at a time to press the halves apart. For some reason mine came apart on one side before the other. A couple of quick taps on the oil drain boss popped the other side out and separated the halves. In this photo I had already removed the compressor housing, which is held on by 6 bolts, and comes off with relative ease.
Care must be taken during this step to ensure you separate the center cartridge from the turbine housing evenly so you don't bind the wheels in the housings, potentially damaging the wheels, in which case you just made yourself a paperweight.
With the center cartridge out, the next step will be to make some index marks on the wheels so you can reassemble it the same way it came apart to preserve balance. I've seen mixed reviews online as to whether the wheels were balanced individually or as a unit from the factory, or even if balance will have an effect on performance. Best to play it safe here. You need a 12 point socket or box-end wrench on the compressor nut, and a 6-point socket on the turbine end of the shaft. Remove the nut, and the compressor wheel should slide off. The shaft and turbine wheel might be trying really hard to stay in the cartridge, this is likely because of the "piston ring" in the exhaust end is acting as a bit of a retaining clip. Just press on the shaft and it'll pop out.
The shaft is likely to be grimy. I used a scotchbrite pad and some acetone to clean mine up. Inspect the shaft to make sure that it doesn't have ridges or grooves from the bearing surfaces. Normally the bearings should take all the wear, and in my case, they did. With the shaft and wheels out of the way, you can now remove the compressor backing plate, which is held on by 4 small bolts. Don't let their size fool you -- mine were in TIGHT with red thread locker, so it took a bit of effort to remove them.
With the backing plate off, you can see the thrust bearing and the oil seal. In my case I didn't have any thrust play but I'm replacing the thrust parts anyway.
I'm currently waiting for my rebuild kit to arrive, according to the tracking number provided by G-Pop Shop it should be here any day.
Okay, maybe it's not that easy, at least not the disassembly part. Think about it -- these turbos are 20 years old and have been subjected to exhaust heat, and their own heat generated from spinning amazingly high RPM.
The first step was to remove the "swingvalve", which includes the exhaust outlet. This Garrett has the larger 2 1/2 inch exhaust opening, instead of the 2 1/4 inch opening in older models. There are 5 bolts holding the swingvalve to the turbine housing, one is hidden inside the swingvalve. I lucked out and all came out with a little penetrating oil. The general consensus seems to be that you require heat to get the bolts out without snapping them off.
After removing the swingvalve and realizing I had no vise to mount the turbo in, I bolted it to a 2x4 which I could clamp down to the workbench through 3 of the swingvalve holes. This is where the fun begins. There are 6 bolts that hold the centre cartridge (including the shaft and bearings) to the turbine housing. These are usually the worst bolts to remove, and clearance is quite limited. I managed to get a thin box-end wrench on 3 of them, the other 3 need an open-end wrench. I soaked the bolts in penetrating oil for quite a long time. I sprayed them daily for several weeks, because again the general consensus is that heat is required for all 6 bolts, and that the housing needs to be heated cherry-red before you can even think about removing them. That cuts out your garden variety propane torch as a source of heat.
Somehow I again lucked out and 5 of the 6 bolts came out without problem, and without heat. Wouldn't you know it, though, that the one bolt that had to be stubborn was one of the ones that needed an open-end wrench. A little heat helped break it free, but nowhere near the amount of heat to turn the housing any colours.
Care must be taken during this step to ensure you separate the center cartridge from the turbine housing evenly so you don't bind the wheels in the housings, potentially damaging the wheels, in which case you just made yourself a paperweight.
The shaft is likely to be grimy. I used a scotchbrite pad and some acetone to clean mine up. Inspect the shaft to make sure that it doesn't have ridges or grooves from the bearing surfaces. Normally the bearings should take all the wear, and in my case, they did. With the shaft and wheels out of the way, you can now remove the compressor backing plate, which is held on by 4 small bolts. Don't let their size fool you -- mine were in TIGHT with red thread locker, so it took a bit of effort to remove them.
I'm currently waiting for my rebuild kit to arrive, according to the tracking number provided by G-Pop Shop it should be here any day.
A quick glamor shot
Over the past few days I've been scrubbing up the parts that didn't make it to the machine shop for cleaning, and painting a few of them. For your enjoyment, here's my valve cover as it is now:
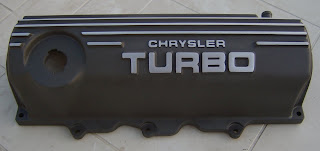
The lighting was poor so you can't tell that it's not black, but Duplicolor "Cast Coat Iron" engine enamel. It's the same colour as the block is, and the intake manifold will be.
The joys of cleaning aluminum
After being quoted $50 per part for bead blasting, I chose to clean my parts myself. The intake, water pump, and the alternator/AC bracket are cast aluminum and were all pretty grimy.
When disassembling the water pump I snapped one of the bolts off in the housing. Yay. I can hardly wait to see what happens next.
When disassembling the water pump I snapped one of the bolts off in the housing. Yay. I can hardly wait to see what happens next.
No longer headless
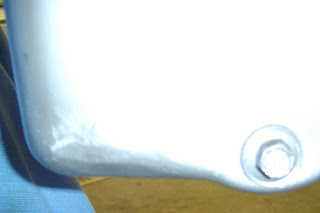
After flipping the engine upright I chased the threads for the headbolts with an old headbolt (re-using these bolts is usually not recommended unless you like changing headgaskets and planing heads on a regular basis) which I cut thin slots into with a Dremel, and after oiling the bolt ran it in to each bolt hole, unscrewed it, cleaned it, repeat until I could thread it in and out all the way with my fingers and the bolt comes out clean. I removed a bit of rust from 4 of the holes, the others came up clean.
The head went on today as well, I used a Mopar Performance "2006" headgasket and Mopar Performance headbolts.
The manifolds didn't go on today like I hoped because the intake is being more difficult to clean than I thought. Tomorrow I think I'm just going to try a powerwasher on it. I know I could still just slap it on and run it, this isn't a show car, blah blah blah... but I want it to at least be clean and nice looking when I get it all together the first time, so it will be easier to keep clean later.
Drawing ever closer...
I ordered my fuel pump today, the online vendor I was planning to buy it from put it on sale for $23 less, I had to jump on that.
More work, again no photos
Okay, I really did intend to take the camera with me tonight but forgot. It's really too bad since I never did get a shot of the bare head as it came back from the machine shop, it did look quite impressive. Tonight I was going to put on my freshly welded up oil pan (thanks Mr. D!) but when I opened the trash bag it was in I realized I had forgotten just how grimy it was (along with the rest of the engine originally) so I set to work degreasing it. I probably should shoot some paint on the welded area anyway to prevent rust. That proved to be quite difficult, and as I left it to soak in degreaser I started to assemble the head.
Starting resulted in finishing. I get carried away so easily.
Starting resulted in finishing. I get carried away so easily.
Progress continues, sans photos
Today I made some good progress, I'm back up to having a shortblock. No photos, was too busy assembling and besides, my hands were too oily to handle the camera.
Slow and not all that steady
About freaking time
Well, I finally got the call from the machine shop saying everything's ready, but for quite a bit more money than I was expecting. Not wanting to wait much longer, and generally preferring to avoid conflict, I just paid the man and picked it all up.
No, that doesn't mean you can push me around... all the time.
Anyway, I have all the parts in the garage again, and I've been slacking a bit on the photographic side of things. Hopefully I'll partly rectify that tonight. All you've missed was painting the block, installing the crankshaft and assembling the pistons to the rods. I didn't put the pistons in yet as one of my rod bearings came to me damaged and I'm waiting for another one to get here.
No, that doesn't mean you can push me around... all the time.
Anyway, I have all the parts in the garage again, and I've been slacking a bit on the photographic side of things. Hopefully I'll partly rectify that tonight. All you've missed was painting the block, installing the crankshaft and assembling the pistons to the rods. I didn't put the pistons in yet as one of my rod bearings came to me damaged and I'm waiting for another one to get here.
And more time passes
The machine shop is still holding my parts hostage. They never did call me about the condition of everything, I had to call them 4 weeks later on a job they said would take 1 week, just cleaning and measuring everything.
I was told it needed far more work than I was prepared to do, and after some discussion it came out that it wasn't "needed" but "suggested" or "a good way to line the machinist's pockets". The work that was necessary included valve guides and a valve job, and planing the head and block deck. I was told that entire process would take 3 days. Now 2 weeks later and they're still not done...
I was told it needed far more work than I was prepared to do, and after some discussion it came out that it wasn't "needed" but "suggested" or "a good way to line the machinist's pockets". The work that was necessary included valve guides and a valve job, and planing the head and block deck. I was told that entire process would take 3 days. Now 2 weeks later and they're still not done...
(Im)patiently waiting...
It's been a while since the last post, I'll try to stay more on top of things. The block, head, pistons/rods and crankshaft are at a machine shop at the moment, I'm waiting to hear the full report on the condition of everything.
Turbo engine overhaul Part 2
Balance shafts are off, pistons are out. In order to get the balance shafts off I needed to get the front seal retainer off so I could access the sprocket and chain, and in order to get the front seal retainer off I needed to get the timing sprocket off.
For some reason known only to an evil Chrysler engineer who's probably still cackling about it, there was a transition from 4 to 5 bolts that hold the accessory drive pulley. With 4 bolts it's easy to use a standard steering wheel puller. With 5 it's more difficult. Here's what I rigged up: I unscrewed the crank sprocket bolt some, bolted the pulley to the sprocket with longer bolts - in this case, the bolts from the intake manifold. The box end wrench is on a nut that has a bolt threaded through it, which is pressing against the head of the crank bolt. There's also a thick washer on there that prevents the nut from just going through the centre hole in the pulley. Holding the nut and tightening the bolt draws the sprocket off. Quick and dirty but it worked.
Once I got the seal retainer off I was faced with another challenge. E-torx bolts on the balance shaft chain sprocket. Turns out a 1/4 inch socket fits closely enough to get those out, then the balance shaft assembly comes off easily giving clear access to the main and connecting rod caps.
All of the rod bearings and journals are in excellent shape. I'm going to replace the bearings regardless. The connecting rods and wrist pins are in good shape, and the pistons, while they can use a good scrubbing, also look pretty good.
The next step is going to be removal of the crankshaft, then the long, slow process of cleaning and inspecting everything, while I save up a little cash to buy the replacement parts.
I can see why these pistons are often referred to as "tuna cans". Nice to see the forged connecting rods and standard size bearings too. Overall I'm happy with the condition inside the engine.
All of the rod bearings and journals are in excellent shape. I'm going to replace the bearings regardless. The connecting rods and wrist pins are in good shape, and the pistons, while they can use a good scrubbing, also look pretty good.
I can see why these pistons are often referred to as "tuna cans". Nice to see the forged connecting rods and standard size bearings too. Overall I'm happy with the condition inside the engine.
The question everyone seems to be asking...
"Why a LeBaron?"
The answer to this is simple: It's an easy to find domestic convertible that's easy to work on, and I've always liked them. Here's how this breaks down:
1) easy to find: this one is obvious. Cars that are easy to find are easy to find parts for, and can generally be bought cheap in the first place. LeBarons are derived from the K-car, along with 95% of Chrysler's lineup at the time. This makes parts and parts cars plentiful.
2) domestic: again, this makes the cost of parts lower.
3) convertible: need I say more?
4) easy to work on: as much as you might not want to hear it, K-cars and their derivatives are by far the easiest FWD cars to work on. Ever.
5) I've always liked them: now that's the part that really matters, right?
The answer to this is simple: It's an easy to find domestic convertible that's easy to work on, and I've always liked them. Here's how this breaks down:
1) easy to find: this one is obvious. Cars that are easy to find are easy to find parts for, and can generally be bought cheap in the first place. LeBarons are derived from the K-car, along with 95% of Chrysler's lineup at the time. This makes parts and parts cars plentiful.
2) domestic: again, this makes the cost of parts lower.
3) convertible: need I say more?
4) easy to work on: as much as you might not want to hear it, K-cars and their derivatives are by far the easiest FWD cars to work on. Ever.
5) I've always liked them: now that's the part that really matters, right?
Turbo engine overhaul Part 1
To make a long story (the first post) short, I'm upgrading a base model 1989 Chrysler LeBaron Convertible to a 2.5L turbo engine and the a520 manual transaxle from the 2.5L TBI and a413 3-speed automatic.
Not that there's anything wrong with that combination. It will likely run forever if you keep oil in it. It's just a little slow for a car this heavy, and therefore boring.
I'm currently in the process of checking the junkyard engine over. It's up on a stand in a friend's garage, where I've torn it down to the shortblock so far. Some observations:
1) Someone's been in this engine before me. I'm not yet sure if that's good or bad. I know this because:
a) the intermediate shaft sprocket mark was mis-aligned according to the other timing sprockets by about 90 degrees. That tells me that someone's at least had the oil pump out at some point.
b) The plated links do not match up with the dots on the balance shafts. That's not the end of the world, but that's not how it would have come from the factory. And no, the balance shafts do not need to be removed to remove the oil pump, and vice versa.
2) This engine is also not original to the donor car. Both the engine block and the transmission case have "89 Dodge 2.5" written on them in paint marker. I'm now dealing with a combination of unknown mileage. Again I don't know if that's good or bad.
3) It looks like this engine might have relatively few kilometers, or at least few kilometers since someone was last in there. Check out that crosshatch!
4) I'm going to use anti-seize compound and stainless fasteners wherever I can. Half of the exhaust manifold studs came out of the head with the nuts, and the exhaust manifold-to-turbo nuts were quite tough. I had a clear shot at 2 of them with the impact gun (which is possibly my favourite tool of them all) but the other two were much more difficult. After soaking for days in penetrating oil, a little ingenuity, a lot of grunting and a shiny new 15mm wrench with lifetime warranty (50% off Mastercraft Maximum wrench sets after Boxing Week!) later, I got the other 2 nuts off.
5) The people at Buck's are F'n A-holes. Yup, I said it. How lazy do you have to be? I think it would actually take less effort to remove the drain bolt from the pan. The location of that hole didn't even drain all the oil out anyway. My plan to deal with this is to pound it out as flat as possible, then either a) get it welded back up or b) jam a bolt through it and give it a nice gob of JB Weld. I would prefer the first option, but I don't exactly have a welder in my back pocket.
6) The turbo is in good shape. There is no in/out shaft play, and minimal (read: about .005" or less) side-to-side play. So much for a good excuse to upgrade to a larger one. The Mitsubishi TE04H that came stock on the 88+ Turbo I engines is pretty small, although it does spool quickly and seem to be good at least to 14 PSI, which I don't plan to exceed anyway.
I don't have more photos showing exactly how far I got at the moment, but like I said I have it down to shortblock right now. I still intend to pull the pistons, and start the slow process of getting everything cleaned. I'm trying to determine where, if anywhere, to take the block to get it checked over, cleaned, honed, etc. as well as the head. At bare minimum I'm going to scrub everything up myself and give a good visual inspection. There were no signs of headgasket failure, past, present, or near future, but I will still check the block deck and head for warpage. There are the usual minute cracks between the valve seats, which seem to be unavoidable on these engines.
When the time comes to re-assemble I'm going to be replacing every seal, plug, o-ring and gasket, along with new rings, main and rod bearings. New oil feed line for the turbo, and new vacuum and fuel hoses. I'll add other parts to this list as I find them to require replacement.
That's all for now, more updates as I feel like posting them.
Not that there's anything wrong with that combination. It will likely run forever if you keep oil in it. It's just a little slow for a car this heavy, and therefore boring.
1) Someone's been in this engine before me. I'm not yet sure if that's good or bad. I know this because:
a) the intermediate shaft sprocket mark was mis-aligned according to the other timing sprockets by about 90 degrees. That tells me that someone's at least had the oil pump out at some point.
b) The plated links do not match up with the dots on the balance shafts. That's not the end of the world, but that's not how it would have come from the factory. And no, the balance shafts do not need to be removed to remove the oil pump, and vice versa.
2) This engine is also not original to the donor car. Both the engine block and the transmission case have "89 Dodge 2.5" written on them in paint marker. I'm now dealing with a combination of unknown mileage. Again I don't know if that's good or bad.
4) I'm going to use anti-seize compound and stainless fasteners wherever I can. Half of the exhaust manifold studs came out of the head with the nuts, and the exhaust manifold-to-turbo nuts were quite tough. I had a clear shot at 2 of them with the impact gun (which is possibly my favourite tool of them all) but the other two were much more difficult. After soaking for days in penetrating oil, a little ingenuity, a lot of grunting and a shiny new 15mm wrench with lifetime warranty (50% off Mastercraft Maximum wrench sets after Boxing Week!) later, I got the other 2 nuts off.
6) The turbo is in good shape. There is no in/out shaft play, and minimal (read: about .005" or less) side-to-side play. So much for a good excuse to upgrade to a larger one. The Mitsubishi TE04H that came stock on the 88+ Turbo I engines is pretty small, although it does spool quickly and seem to be good at least to 14 PSI, which I don't plan to exceed anyway.
I don't have more photos showing exactly how far I got at the moment, but like I said I have it down to shortblock right now. I still intend to pull the pistons, and start the slow process of getting everything cleaned. I'm trying to determine where, if anywhere, to take the block to get it checked over, cleaned, honed, etc. as well as the head. At bare minimum I'm going to scrub everything up myself and give a good visual inspection. There were no signs of headgasket failure, past, present, or near future, but I will still check the block deck and head for warpage. There are the usual minute cracks between the valve seats, which seem to be unavoidable on these engines.
When the time comes to re-assemble I'm going to be replacing every seal, plug, o-ring and gasket, along with new rings, main and rod bearings. New oil feed line for the turbo, and new vacuum and fuel hoses. I'll add other parts to this list as I find them to require replacement.
That's all for now, more updates as I feel like posting them.
In the beginning...
In April of 2007 my wife and I determined we needed a second car. I had a job where I needed a vehicle at work every day, so it made it difficult for her to either a) be called in to work or b) go shopping, etc. We found a few cars that were more rust than car or barely ran. Then one day my wife happened to mention to a co-worker that we were looking and she said she had an 89 LeBaron convertible sitting on her driveway she wanted to get rid of.
My wife called me and told me about that and I was more or less sold right then. I've always loved the J-bodies, and wanted a convertible for years.
We went out to go see it one night. That time of year it was still getting dark early. The battery was drained so they had put it on charge that afternoon. We did the usual walk-around and poked and prodded at the imperfections like the rust spots and the splits in the top.
The previous owners told us it sat on the driveway for so long because of suspected transmission issues, and that the problem was described to them as a bearing in the differential. I took the car for a quick test drive and felt the shudder they told me about. It was pretty bad. It felt like I was constantly driving on a washboard road. I was a little disappointed and drove back to their house. Then I got out and I saw the "donut spare" was on the front. That didn't help matters, I'm sure.
We left that night saying we'd think about it. I was a little turned off, but it stayed in the back of my mind. Finally a week later it had tortured me enough that I had to go pick it up. I went back with a friend of mine who could give me a second opinion. After his thumbs-up we took it for another test drive, offered the owner a little less than the asking price, and took her home.
183,000 miles on the clock, on an engine rebuilt 70,000 miles ago, supposedly. There is the usual 80's Chrysler clearcoat failure on the trunk and surrounding area, and a bit at the tops of the doors. The passenger's door has some rust on it, as do the quarter panels just above the tail lights on both sides. There is also some floorpan rot on both sides, particularly around the parking brake cable. This is often seen on these 80's Chryslers.
Oddly enough, it has almost power nothing. It has power windows and top, which they all have.
The only option was the airbag, which will become a bit of a thorn in my side in later posts.
Under the hood is the base engine, a 2.5L TBI and a 3-speed automatic, aka the a413. The first thing I did was change the oil and replace tune-up parts ie spark plugs, cap, rotor, PCV valve, air filter, and the coil as the case was rusty.
I discovered the source of the vibration wasn't the transmission at all, but a broken front motor mount and a sloppy inner CV joint. I replaced both and saw a huge improvement. At the same time I adjusted the bands in the transmission and re-centered the engine. After that, I slowly replaced the following parts - front & rear brake pads and rotors, ball joints, outer tie rod ends, EGR valve, AIS motor, and all vacuum lines.
Then, in September everything changed. I found a wrecked LeBaron in the junkyard with the engine and transmission combo I wished this one had: a 2.5L Turbo 1 and the a520 5-speed manual. The car was untouched, with the exception of the radio having been taken out. Over the next couple of days I took the doors as they were rust-free and had power mirrors and locks, the rear quarter windows as the seals are in much better shape than mine, the door seals, a couple of convertible-specific trim pieces, and the shifter boot/cover plate as that is also convertible-specific, as a just-in-case part.
3 weeks later I got the go-ahead from the wife to pull the engine, transmission, and any other parts necessary to do the conversion. She probably agreed just to shut me up. The day we picked to pull the parts was less than ideal. A friend of mine came up to the city to help, as well as to look (unsuccessfully) for parts for his car. That day had a high wind, heavy rain and near-freezing temperatures. We spent what seemed like 6 hours out there in that, while in reality it was probably more like 3. We picked clean what we could, I had to leave the shifter, shift cables, clutch pedal and cable behind, hoping nobody would touch them. We just had to get out of there, we were cold, soaked and hungry.
My co-worker offered up some garage space based on the understanding that I'd help him in his garage with his stuff from time to time. That's an offer I can't refuse. Otherwise my shiny new toys would be sitting outside under a tarp over the winter and I would still not have anywhere to do the work.
Time passes... stay tuned for the more exciting part -- engine rebuilding and ultimately converting a TBI/auto car to a turbo/5-speed!
Subscribe to:
Posts (Atom)